Wichtige Erkenntnisse:
- Der Einsatz von digitalen Zwillingen kann den Mangel an qualifizierten Arbeitskräften in der Fertigung ausgleichen
- Digitale Zwillinge bieten einen fruchtbaren Nährboden für die Ausbildung neuer Mitarbeiter in der Fertigung und mildern gleichzeitig andere Probleme
Vollständiger Artikel:
Eine NAM-Umfrage zum vierten Quartal 2023 unter kleinen Fertigungsunternehmen mit weniger als 50 Mitarbeitern und mittelgroßen Firmen mit 50-499 Mitarbeitern ergab, dass mehr als 71,4 % der Befragten die Unfähigkeit, Mitarbeiter anzuwerben und zu halten, als ihre größte Herausforderung bezeichneten. Erschwerend kommt hinzu, dass die geburtenstarken Jahrgänge schnell in den Ruhestand gehen und somit große Lücken bei den Arbeitskräften und wichtigen Qualifikationen hinterlassen. Und das ist nicht nur ein Problem in Nordamerika. Der geopolitische Stratege und Hauptredner Peter Zeihan stellte in einem Interview auf der aPriori 2023 Manufacturing Insights Conference (MIC) fest, dass Europa nach China die am schnellsten alternde Bevölkerung hat.
Was kann getan werden, um den Fachkräftemangel in der Fertigung einzudämmen? Wie können Hersteller mehr qualifiziertes Personal entwickeln und gleichzeitig mit weniger mehr erreichen?
Der Schlüssel, um diese Erfahrung zu ersetzen, liegt in der Automatisierung durch digitale Zwillinge. Durch den digitalen Faden verbunden, ermöglichen digitale Zwillinge den Herstellern, wichtige Informationen zu erschließen, die nicht nur als Lehrmittel dienen, sondern auch den Fachkräftemangel kurzfristig kompensieren können. Auf diese Weise können Hersteller ihre Unternehmen umgestalten und ihre Agilität, Markteinführungszeit und Rentabilität erhöhen.
5 Möglichkeiten, den Fachkräftemangel in der Fertigung zu kompensieren
Durch die Nutzung digitaler Zwillinge können Hersteller ihre qualifizierten Arbeitskräfte aufstocken und kritische Probleme bei der Produktentwicklung angehen. Lassen Sie uns fünf Möglichkeiten untersuchen:
- Unterstützung einer schnelleren Qualifizierung von Konstrukteuren. In einer idealen Welt hätten neue Konstrukteure den Luxus, mehrere Wochen oder Monate lang alle Facetten der Produktion kennenzulernen, um die Herstellbarkeit ihrer Entwürfe zu gewährleisten. Obwohl dies eine wertvolle Erfahrung darstellt, ist es für die meisten Hersteller nicht mehr praktikabel. Vielleicht befinden sich ihre Produktionsanlagen nicht in der Nähe des Konstrukteurs. Außerdem bedeutet mehr Zeit im Feld weniger Zeit für die Konstruktion. Die Bereitstellung digitaler Lösungen, die bereits in einem frühen Stadium des Prozesses Einblicke in die Konstruktion ermöglichen, hilft neueren Konstrukteuren, schneller Erfahrungen zu sammeln. Diese Einblicke geben ihnen ein klareres Verständnis der Produktionsaspekte ihres Entwurfs, einschließlich Beschaffung, Kosten und Produktionsauswirkungen. Das Ergebnis ist ein besseres Produkt, mehr Innovation und weniger Iterationen und Verzögerungen bei der Markteinführung.
- Optimieren Sie den Kostenprozess und bauen Sie institutionelles Wissen auf. Eine kürzlich durchgeführte Umfrage der Boston Consulting Group (BCG) ergab, dass 65 % der Führungskräfte weltweit das Gesamtkostenmanagement als sehr wichtig einstufen und ihm in den Bereichen Lieferkette und Fertigung Priorität einräumen, wobei 52 % den Arbeits-/Nichtarbeitsgemeinkosten Priorität einräumen. Die Kosten sind das Herzstück der Produktentwicklung. Traditionell wurden sie von vielen Personen und mit zeitaufwändigen, uneinheitlichen Tabellenkalkulationen ermittelt. Hinzu kommt, dass das im Laufe der Jahre angesammelte institutionelle Kostenwissen oft mit den ausscheidenden Fachkräften verloren geht. Die Automatisierung führt zu einer höheren Kostengenauigkeit und stellt sicher, dass das gesamte Produktentwicklungsteam mit einer einzigen Datenquelle arbeitet und in jeder Facette der Produktentwicklung wichtige Erfahrungen sammelt, um sein Wissen zu erweitern. Entdecken Sie, wie Carrier die Kostenkalkulation automatisierte und dabei Millionen von Dollar einsparte und sein Produktentwicklungsteam in die Nutzung von aPriori.
- Effizientere und profitablere Beschaffung. Die Beschaffung von Materialien erfordert langwierige Verhandlungen und Zeit, um die richtigen Lieferanten zum richtigen Preis zu finden. Dies ist in der Regel eine erworbene Fähigkeit. Digitale Lösungen helfen dabei, solche Möglichkeiten aufzudecken und die Beziehungen zu den Lieferanten zu stärken, um die Effizienz, die Zusammenarbeit und die Verhandlungsführung zu verbessern. Neue Beschaffungsteams können digitale Zwillinge nutzen, um ein tieferes Verständnis für den Lebenszyklus der Produktentwicklung zu erlangen und ein klareres Bild davon zu bekommen, welche Materialien und Komponenten effizienter und profitabler beschafft werden können.
- Reduzieren Sie die Zeit für die Angebotserstellung und rationalisieren Sie den RFQ-Prozess. Die Angebotserstellung ist ein mühsamer und zeitaufwändiger Prozess, bei dem oft unzählige Kunden, Designs und Komponenten verwaltet werden müssen. Ohne einen automatisierten, rationalisierten Angebotsprozess müssen die Hersteller das Rad bei jedem Angebot neu erfinden. Der Einsatz digitaler Zwillinge (d. h. digitaler Fabriken) ermöglicht es Herstellern, die Fertigung in einer digitalen Fabrik zu simulieren, die so konfiguriert ist, dass sie ihren individuellen Fähigkeiten und ihrer Kostenstruktur entspricht. Greener-Angebotsteams können Simulationsinputs leicht anpassen, um spezifische Produktparameter des Kunden widerzuspiegeln, so dass Kostenmodelle für neue Anfragen leicht angepasst werden können und ein rationalisierter Lieferantenangebotsprozess aufgebaut werden kann. Sehen Sie, wie sich die Gesamtgewinnrate eines aPriori-Kunden von 15% auf 68% verbessert hat.
- Automatisieren Sie den Ersatz erfahrener Fertigungsingenieure, die knapp sind. Die Pandemie hat gezeigt, wie schnell sich ein Mangel an Arbeitskräften auf das Geschäft auswirken kann. Die Automatisierung rudimentärer, sich wiederholender Aufgaben entlastet erfahrenes Personal, das sich auf komplexere, technische Aufgaben konzentrieren kann. Angesichts der massiven Abwanderung der Babyboomer, die in den Ruhestand gehen, wird die Notwendigkeit der Automatisierung immer wichtiger. Darüber hinaus kann die digitale Fabrik die physische Produktion nachbilden, so dass auch weniger erfahrene Konstrukteure und andere Produktentwicklungsteams über wichtige Daten verfügen, um das Design zu simulieren, alle Faktoren wie Werkzeuge und Arbeitspläne zu untersuchen, gegebenenfalls Anpassungen vorzunehmen und in der digitalen Fabrik mit dem zu korrelieren, was sie in der tatsächlichen Fertigung sehen werden. Erfahren Sie, wie ein Unternehmen die digitale Fertigungssimulation nutzte, um die Herstellbarkeit und Kostenmodellierung zu standardisieren.
Digitale Zwillinge ermöglichen eine schnellere Einarbeitung von Mitarbeitern in der Fertigung
Digitale Lösungen können weniger erfahrene Mitarbeiter in der Fertigung schneller einarbeiten. Digitale Zwillinge können zum Beispiel bei der Schätzung von Teilen eingesetzt werden, um Produktentwicklungsteams bei der Anpassung von Parametern an die tatsächliche Fertigung zu unterstützen. Dadurch lernen sie und erhalten Antworten von der Lösung. Infolgedessen werden sie beginnen, der Lösung während der gesamten Produktentwicklung zu vertrauen.
Die regelmäßige Aktualisierung von Daten (Kosten, Beschaffung, Herstellungsverfahren usw.) ist ebenfalls von entscheidender Bedeutung, um Aktualität und Genauigkeit zu gewährleisten. Jüngeres Personal erlangt schneller mehr Wissen und Erfahrung, und alle Produktentwicklungsteams verfügen über einen standardisierten, gemeinsamen Datensatz, mit dem sie arbeiten können. Das Ergebnis ist eine schnellere Umschulung, eine größere betriebliche Effizienz, eine Minimierung des Risikos und höhere Gewinne.
Beeinträchtigt der Mangel an Arbeitskräften die Produktivität?
Erfahren Sie, wie Woodward die digitale Technologie zur Lösung des Problems nutzte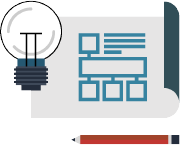
Abonnieren Sie den aPriori Blog
Mit technologiebasierten Lösungen ist eine strategische Materialbeschaffung möglich
25 September 2024Verwandeln Sie Meetings zur Überprüfung des Produktdesigns in schnelle Designvalidierungen
17 September 2024Wie KI-Tools die Kosten für die Produktentwicklung und die Markteinführungszeit senken
22 August 2024