Ich muss die Kosten eines Teils optimieren. Wo fange ich damit an?
Die deutliche Mehrheit der Kosten eines Teils (70 % oder mehr) lassen sich nach Abschluss der Designphase grundsätzlich nicht mehr ändern. Wenn die Konstruktion abgeschlossen ist, haben Mitarbeitende in der Produktion oder Beschaffung nur noch sehr wenige Spielraum, Teilekosten zu optimieren. Deshalb ist eine effektive „Design for Manufacturing“-Kostenmodellierung eine unerlässliche Voraussetzung bei der Optimierung der Teilekosten. Konstrukteur*innen müssen in der Lage sein, die Kosten von Designalternativen zu berechnen, während ein Produkt sich noch in der Konzeptionsphase befindet.
Aber wie lassen sich die wichtigsten Kostentreiber des Designs eines bestimmten Teils wirklich in der Konzeptionsphase prognostizieren?
Die kurze Antwort lautet: Je besser die Tools sind, mit denen sich die Herstellbarkeit von Designalternativen beurteilen lässt, um so effektiver können kostenwirksame Designentscheidungen getroffen werden. Tabellen und andere Tools, die sich auf historische Kalkulationen stützen, sind ein guter Ausgangspunkt. Doch simulierte „digitale Fabriken“ wie die von aPriori liefern einen viel detaillierteren, agilen Ansatz, Designentscheidungen in Verbindung mit Kostenergebnissen zu treffen.
In diesem Blogartikel beantworten wir die obige Frage ausführlich und ziehen einige konkrete Beispiele aus der Praxis heran, um die Grundsätze des „Design for Manufacturing“-Ansatzes zu verdeutlichen.
Die Notwendigkeit für „Design for Manufacturability“-Erkenntnisse
Stellen wir uns vor, ein Konstrukteur hätte Zugriff auf präzise Orientierungshilfen zu zentralen Kostentreibern eines spezifischen Designs. Orientierungshilfen dazu, welchen Einfluss Rohmaterialien, Konversion (die Kosten der Verwandlung dieses Rohmaterials in ein Teil), Routing und weitere Herstellbarkeitsfragen auf die Kosten haben.
Damit ließe sich ganz genau verstehen, auf welche Weise Teile neu konstruiert werden könnten, um eine höhere Kosteneffizienz zu erzielen. Und das ist noch nicht alles. Mit diesen Orientierungshilfen könnten bereits bei der erstmaligen Entwicklung eines Teils kostenwirksame Designentscheidungen getroffen werden.
Um die transformative Auswirkung der erweiterten Kostenmodellierung für die Fertigung wirklich zu verstehen, ist es sinnvoll, die ganze Bandbreite der Faktoren zu betrachten, die in Hinblick auf die Endkosten eines Teils eine Rolle spielen. Die unten stehende Liste erhebt keinen Anspruch auf Vollständigkeit, sondern soll darstellen, wie viele Faktoren bei einem wirklich soliden Kostenmodell berücksichtigt werden müssen.
Einige der zentralen Kategorien der Teilekosten schlüsseln wir unten weiter auf. Die Einzelheiten können deutlich variieren, aber diese grundlegenden Kostenkategorien gelten für alle Teile – ob aus Feinblech oder Kunststoff, ob gegossen oder maschinell gefertigt.
Übersicht der wichtigen Kostenkategorien
Direkte + variable Kosten:
Beide dieser Kategorien beschreiben Kosten, die mit den Grenzkosten der Produktion jedes zusätzlichen Teils in Zusammenhang stehen.
Haupttreiber von Materialkosten
- Materialtyp
- Materialbestandsgröße (Standard oder Nicht-Standard)
- Materialausnutzung
- Spezielle Kornorientierungen (z. B. enge Biegungen eines Teils könnten der Grund sein, warum das Teil beim Ausstanzen nur in eine Richtung ausgerichtet werden kann)
Haupttreiber von Lohn- und Gemeinkosten
- Zyklusdauer, um das Teil zu produzieren. Zu beachten ist, dass möglicherweise mehr als eine Maschine genutzt wird, um ein Teil zu fertigen.
- Wie oft eine Einstellung erfolgen muss – eine oder mehrere Maschinen.
- Art und Größe der Maschine/n, die für die Produktion des Teils genutzt wird/werden
- Alle sekundären Prozesse – Lackierung, Hitzebehandlung usw.
Indirekte/periodische Kosten:
Diese Kosten haben einen Einfluss auf die Gesamtrentabilität, doch marginale Produktionsänderungen wirken sich nicht unbedingt unmittelbar darauf aus. Ein Werk hat beispielsweise grundlegende Wartungskosten, unabhängig davon, wie viele Teile über einen gewissen Zeitraum dort gefertigt werden. Für eine Analyse müssen diese Kosten mit spezifischen unterstützenden Funktionen in Zusammenhang stehen und auf alle produzierten Teile umgelegt werden.
Zentrale werksbezogene Kostentreiber
- Energiekosten
- Heizung und Kühlung des Werks
- Reinigung und Wartung
- Beschaffung, Fertigung, Engineering, Versand und Empfang sowie weitere unterstützende Geschäftsfunktionen
Administrative Kostentreiber
- Geschäftsführungskosten
- Ausgaben für Vertrieb, Marketing und Geschäftsentwicklung
- Technologie-Support, z. B. IT-Mitarbeitende oder -Services
Investitionsausgaben (CAPEX) und/oder Einmalkosten
- Dazu gehören beispielsweise Erstinvestitionen in Produktivkapital wie Formen, Stanzwerkzeuge, Bearbeitungsvorrichtungen, Schweißvorrichtungen usw.
- Die Kostenbelastung von Investitionsausgaben ist abhängig von der Komplexität des Teils, der Anzahl der Kavitäten, der Anzahl der Teile in der Lebensdauer des Werkzeugs usw.
Wie können Konstrukteure diese Vielzahl von Faktoren bei der Konzeption oder Neugestaltung eines Teils wirklich realistisch berücksichtigen?
Der unerlässliche erste Schritt der Kostenoptimierung ist die Erstellung eines Modells für die Teilekosten. Mit traditionellen Tools ist es allerdings sehr schwer, eine robuste Kalkulation vorzunehmen. Metriken wie das Kosten-Gewicht-Verhältnis eignen sich als Plausibilitätsprüfung bei ineffizienten Designentscheidungen, liefern aber keine echten Erkenntnisse zu den Zusammenhängen zwischen Design und dem komplexen Zusammenspiel der oben genannten Faktoren.
Um diese Herausforderung zu bewältigen, entwickeln viele Unternehmen Tabellenkalkulationen oder spezifische Software, um Wissen aus früheren Kalkulationen zu erfassen und auf das Design neuer Teile anzuwenden. Diese Tools liefern eine akzeptable Kostenschätzung, die im Designzyklus verwendet werden kann.
Dafür ist eine durchgängige, zuverlässige Methode für die Berücksichtigung von Herstellbarkeit erforderlich. Viele Unternehmen beschäftigen spezielle Manufacturing Engineers, die Kostenkalkulationen für die Konstrukteur*innen erstellen. In ihrer einfachsten Form können diese Kalkulationen zumindest ein grobes Kostenziel ergeben. Idealerweise geht sie jedoch weit darüber hinaus.
Eine detailliertere Aufstellung liefert Konstrukteur*innen deutlich nützlichere Informationen, um tatsächlich einen Design-to-Cost-Ansatz zu verfolgen.
Die Bedeutung des Zusammenhangs zwischen den einzelnen Designentscheidungen zeigt sich besonders in der gesamten Kategorie der direkten/variablen Kosten. Während Konstruktionsentscheidungen periodische Kosten langfristig beeinflussen können, konzentrieren wir uns in diesem Blogartikel auf die direkten Kosten. Denn hier zeigen sich in der Regel die dramatischsten Auswirkungen.
Ein genauer Blick auf echte Erfolgsgeschichten: Digitale Fertigungssimulation nutzen, um Unwirtschaftlichkeit zu identifizieren
Im weiteren Verlauf betrachten wir einige spezifische Beispiele. Während diese Beispiele mithilfe der digitalen Fabriken von aPriori generiert wurden, die auf einer simulierten Produktion zur Modellierung des „digitalen Zwillings“ eines Teils basieren, gilt der Prozess an sich auch für traditionelle Kalkulationstools wie Tabellen.
Kalkulationen müssen nicht perfekt sein, aber zuverlässig. In der Designphase muss der absolute Wert der Kalkulation nicht exakt sein; eine gute Annäherung ist ausreichend. Sie müssen beispielsweise wissen, dass 20 % der Kosten dieses Teils mit dem Material in Zusammenhang stehen und 65 % mit der Konversion. Während diese Summen bei der endgültigen Produktion variieren können, sind sie eine nützliche Orientierungshilfe für die Priorisierung von Kostenoptimierungsprojekten. Sie können damit Zeit sparen, da Sie so keine Veränderungen verfolgen, die nur sehr geringe Auswirkungen auf die Kosten haben.
Eine umfassende digitale Fertigungssimulation wie die von aPriori gibt Produktentwickler*innen die Möglichkeit, viel schneller zu arbeiten. Die Software kann automatisch die effizienteste Fertigungsmethode für ein Teil ermitteln und gleichzeitig beinahe sofort Kostenkalkulationen für neue Designalternativen liefern.
Materialkosten – Beispiel 1: Lüftungsgehäuse aus Feinblech für Lkw
Beginnen wir mit einem Beispiel aus der Praxis – einem Lüftungsgehäuse aus Feinblech für einen Lkw. In dem Screenshot ist zu erkennen, dass das Material 88 % der Kosten dieses Teils ausmacht. Um die Materialkosten zu senken, können Sie entweder
- das Material mit einem günstigeren Material ersetzen (die Veränderungen müssen jedoch weiterhin die funktionalen Belastungsanforderungen erfüllen)
- weniger Material verwenden, indem Sie das Gehäuse dünner gestalten und mit einer Rippenverstärkung versehen, oder indem sie die Materialnutzung verbessern, um Abfall zu reduzieren.
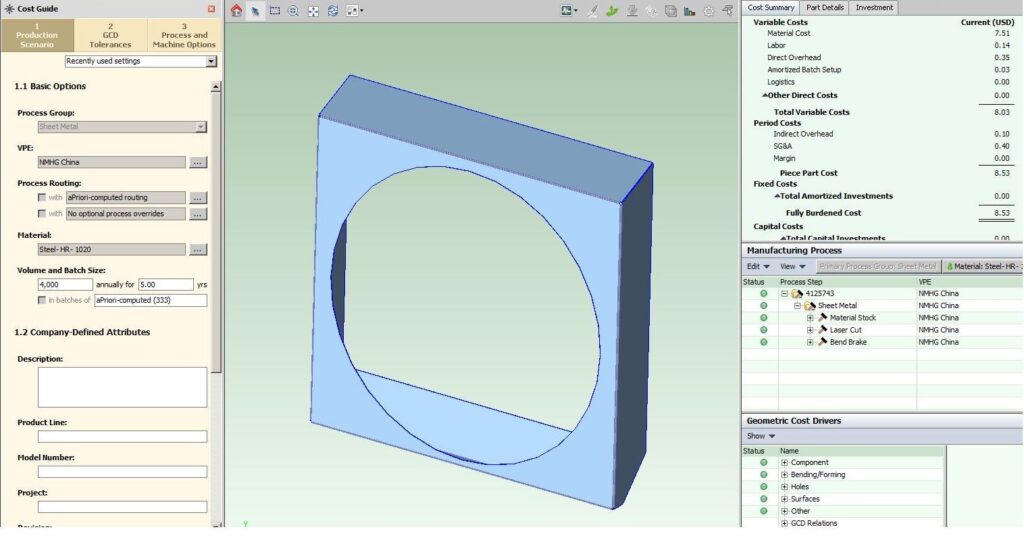
Der für die Designveränderung verantwortliche Konstrukteur erkannte, dass ein so großer Teil der Kosten mit den Materialentscheidungen in Verbindung stand, dass er die Fertigungskosten des Teils (Konversionskosten) erhöhen konnte, um noch höhere Materialeinsparungen zu erzielen. Er machte sich also daran, den Fußabdruck des Teils zu reduzieren, ohne die Größe der Öffnung oder die Steckstellen des Teils zu verändern. Der nächste Screenshot zeigt die ultimative Lösung.
Während Lohn- und Gemeinkosten von 0,49 Dollar-Cent auf 0,53 Dollar-Cent stiegen, sanken die Materialkosten von 7,51 US$ auf 5,63 US$ – eine Differenz von 1,88 US$! Für ein Teil, das in zehntausenden Lkw Anwendung findet, war diese Verbesserung die Mühe wert.
Dies ist ein großartiges Beispiel dafür, wie eine zuverlässige Kostenkalkulation wirklich nützlich für die Priorisierung von Neukonstruktionen sein kann. Ein guter Kostenvektor (steigen oder sinken die Kosten, um viel oder um wenig?) ist ausreichend. Was hätte der Konstrukteur beispielsweise anders gemacht, wenn die „Konversionskosten“ stattdessen auf 0,65 Dollar-Cents gestiegen wären? Oder wenn die Materialkosten tatsächlich nur um 1,50 US$ anstatt 1,88 US$ gesunken wären? Das Endergebnis wäre dasselbe: eine erfolgreiche Neukonstruktion.
Materialkosten – Beispiel 2: Kunststoffsitz
Der Hersteller des unten gezeigten Sitzes produziert etwa 200.000 dieser Sitze pro Jahr. Das digitale Fertigungskostenmodell zeigte, dass der überwiegende Anteil der Kosten dieses Teils mit 67 % in den Materialkosten liegt.
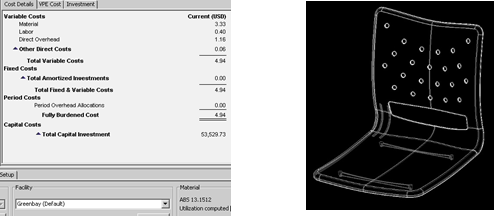
Die Konstrukteurin, die dieses Teil neu gestaltete, hatte zwei Optionen:
- Günstigeres Material zu verwenden. Hinweis: Hätten die „Konversionskosten“ den Großteil der Kosten ausgemacht, wäre ein Material erstrebenswert gewesen, dass schneller abkühlt und damit die Zyklusdauer und die Kosten der Herstellung verringert.
- Weniger Material zu nutzen, ohne dabei die Integrität des Sitzes zu beeinträchtigen.
Die Konstrukteurin analysierte verschiedene Alternativen, hier zwei Beispiele:
Zunächst schrägte sie die Dicke des Kunststoffs ab, von der oberen Kante der Lehne bis auf etwa 2/3 der Höhe sowie vom Rand des Sitzes über etwa die Hälfte des Sitzteils. Mit dieser Veränderung wurde die durchschnittliche Dicke von 0,18 Zoll auf 0,15 Zoll reduziert. Zu beachten ist auch, dass damit Material-, Lohn- und Gemeinkosten ebenfalls reduziert wurden: Denn je dünner das Teil, desto schneller kühlt es aus. Dieser doppelte Nutzen führte zu einer Kostensenkung um 0,95 Dollar-Cent bei einem 5 US$-Teil.
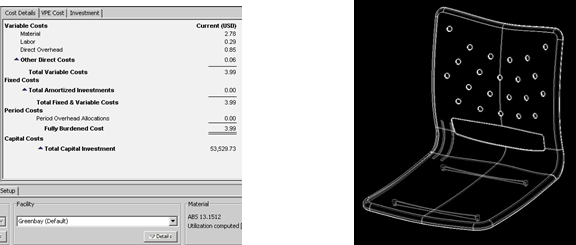
Im Rahmen der zweiten Veränderung wurde das Loch in der Lehne leicht vergrößert, von einer Höhe von ursprünglich 5 Zoll auf 6 Zoll. Diese Veränderung führte nur zu einer Kostenreduzierung um wenige Cent und war es somit nicht wert, potenzielle Qualitätsprobleme oder eine Verringerung der Bequemlichkeit des Sitzes zu riskieren. Direkt bei der Entwicklung Kostenfeedback in Echtzeit zu erhalten, gibt Ihnen die Möglichkeit, diese falschen Fährten sehr früh im Prozess zu erkennen.
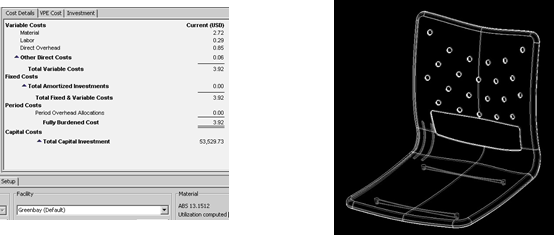
Weitere Beispiele und Tipps zu Materialkosten
- Achten Sie auf die Enge des Biegeradius eines Feinblech-Teils. Bei einem Kunden wurden, unabhängig vom Teil, die Biegeradien auf denselben Wert gesetzt. Für einige der Teile betrug dieser Radius weniger als die Hälfte der Dicke des Teils. Ich fragte den Produktionsingenieur, ob es ihm schwer fiel, diese Anforderung zu erfüllen. Er sagte: „Nein, wir vergrößern den Biegeradius einfach, wir kennen die Absicht des Designs.“
Dieser Vorgehensweise funktionierte, bis die Arbeitsbelastung des Werks so hoch wurde, dass man Teile kaufte oder andere interne Werken im ganzen Land einbezog. Die Teile wurden viel teurer, weil sie lotrecht zur Biegung ausgerichtet werden mussten. Das schränkte die Schachtelungsflexibilität des Teils ein, sodass mehr Material verwendet wurde. Eine Produktionssimulation (wie aPriori) zeigt automatisch auf, dass eine Biegung zu eng ist, und empfiehlt einen Minimalwert für den Biegewinkel. - Manchmal kann eine geringe Abweichung von Standard-Rohmaterialgrößen sehr teuer werden.Ein Fortune-100-Kunde erzählte folgende Geschichte: Das Unternehmen konzipierte ein neues Schwungrad für die größere Version einer Maschine. Das Design von Schwungrädern ist unkompliziert und man erwartete, dass die Kosten proportional zur Vergrößerung steigen würden. Doch sie waren weitaus höher – mit einer Steigerung von fast 100 anstatt der erwarteten 30 Prozent.
Man nahm zunächst an, der Zulieferer habe ein überzogenes Angebot eingereicht. Bei der Überprüfung wurde jedoch festgestellt, dass der Zulieferer ein spezielles Schmiedeteil kaufen musste, um die Vorgaben zu erfüllen, oder mit dem nächstgrößeren Standardstab beginnen musste. Beides hatte unverhältnismäßig große Auswirkungen auf die Kosten. Mit einer Reduzierung des Durchmessers von nur wenigen Millimeter konnte das Problem aus der Welt geschafft werden, und die Trägheitsmarge des finalen Designs war immer noch ausreichend.
Konversionskosten – Beispiel
Widmen wir uns nun der Konversion. Konstrukteur*innen treffen Entscheidungen, die verschiedenste Aspekte der Konversionskosten betreffen.
Diese Beispiele verdeutlichen das.
- Lohnkosten: Proportional zur Zyklusdauer wirkt sich auch die notwendige Kompetenz zum Betrieb der Maschine auf den Lohn des Maschinenführers aus. Der Maschinenführer einer 5-achsigen CNC-Fräse verdient mehr als der Maschinenführer einer 3-achsigen Fräse.
- Einstellungs-/Einrichtungskosten: Anzahl der Maschinen, die eingestellt werden müssen, und Häufigkeit der Einrichtung der Teile. Bei der Bestimmung der Auswirkungen der Einstellungskosten pro Produkt spielt das Volumen eine große Rolle.
- Direkte Gemeinkosten: Diese steigen und sinken ebenfalls proportional zur Zyklusdauer und der Art und Größe der Maschine.
Ein Konstrukteur wurde beauftragt, die Kosten für ein Teil wie unten abgebildet zu reduzieren (dieses Szenario basiert auf einer wahren Begebenheit). Eine schnelle Prüfung der Kosten zeigte, dass sich das Verhältnis von Material- und Konversionskosten auf etwa 40:60 belief. Daraus ergab sich, dass es in beiden Bereichen Potenzial für eine Kostenreduzierung geben könnte.
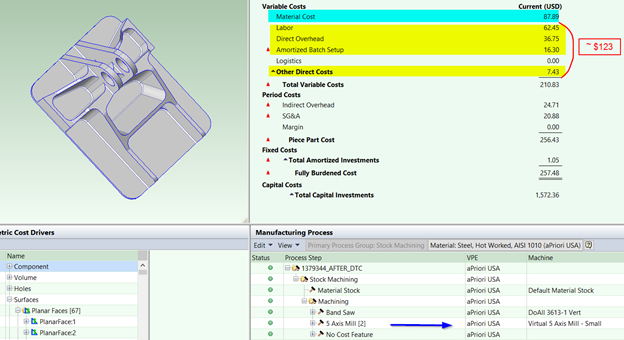
Der Konstrukteur stellte außerdem fest, dass es sich um ein Teil mit relativ geringem Volumen (300 Stück pro Jahr) handelte und es daher als maschinell bearbeitetes Teil eingekauft wurde. Während das Teil an sich nicht besonders komplex war, erforderten die mehrfachen Schrägen auf der Oberfläche die Nutzung einer 5-achsigen Fräse (anstatt einer vergleichsweise günstigen 3-achsigen Fräse).
Es gab folgende Möglichkeiten:
- Neugestaltung des Teils, um die Komplexität zu reduzieren und die Fertigung auf eine günstigere Maschine zu verlagern
- Genauere Analyse der Treiber der Bearbeitungskosten und wie diese Kosten in der Designphase reduziert werden können
- Berücksichtigung alternativer Fertigungsprozesse für das Teil, wenn dies vielversprechend erscheint
Mithilfe einer Fertigungssimulation für die Kostenanalyse stellte der Konstrukteur fest, dass die Materialausnutzung nur bei 11 % lag. Das bedeutete, dass fast 9 von 10 kg zu Abfall wurden. Eine genauere Untersuchung ergab, dass der Großteil der Produktionskosten des Teils wie erwartet in der Bearbeitung lagen, allerdings in der Rohbearbeitung, nicht in der Endbearbeitung. Damit zeigte sich, dass die gewünschte Endkontur in der Rohbearbeitung sowohl hohe Material- als auch hohe Fertigungskosten mit sich brachte.
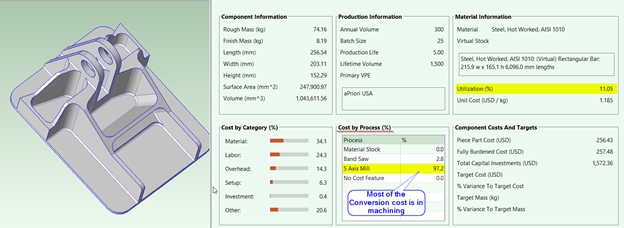
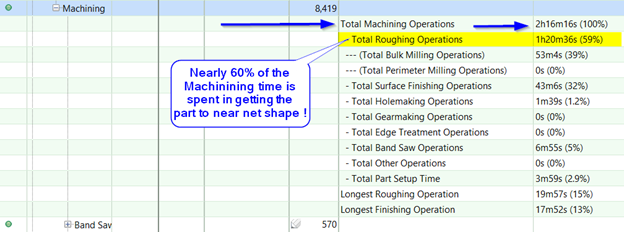
Aufgrund des relativ geringen Produktionsvolumens von 300 Stück pro Jahr war das Teil als maschinell bearbeitetes Teil vorgesehen. Basierend auf diesen Ergebnissen wurde jedoch entschieden, ein Sandgussverfahren für dieses Teil in Betracht zu ziehen. Um festzustellen, ob sich die Wiederholung der Design- und Ermüdungsanalyse für ein Gussverfahren lohnen würde, erstellte man eine Kalkulation für die Produktion des Teils im Sandgussverfahren.
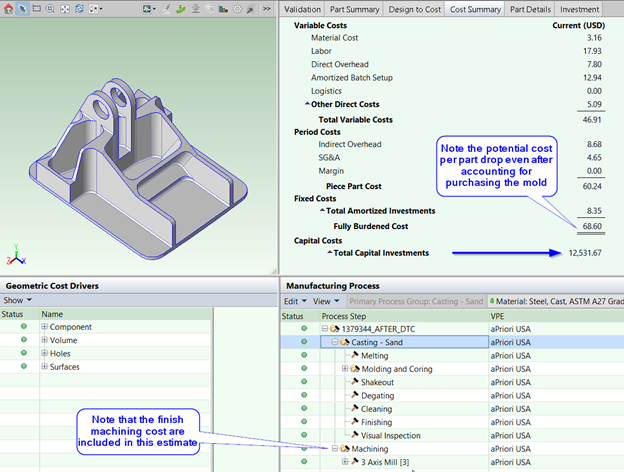
Nach dieser Analyse der Kostendifferenz – etwa 190 US$ pro Teil bei 300 Stück, was eine potenzielle jährliche Einsparung von 57.000 US$ bedeutete – wurde das Teil neu konzipiert und als Gussstück eingekauft, um maßgebliche Einsparungen zu realisieren.
Stellen Sie sich andererseits vor, dass dieses Teil sich aufgrund der Belastungs- und Ermüdungsanforderungen nicht für ein Gussverfahren eignet, so wie das unten gezeigte Teil. Der Prozess für die Reduzierung der Kosten dieses Teils ist ähnlich, allerdings müssen die Bearbeitungskosten analysiert werden (und einige Teile könnten auch stranggepresst sein).
In diesem Fall betrachten wir potenzielle Herstellbarkeitsprobleme, die uns womöglich teuer zu stehen kommen. Ein digitales Simulationstool wie aPriori bezieht die Produktionsmethoden ein, mit denen das Teil tatsächlich hergestellt werden soll. Dabei werden Eigenschaften erfasst, die die Produktion komplex machen. Bei Kunststoff- oder Druckgussverfahren könnten das die fehlenden Entformungsschrägen sein, oder zu dicke oder zu dünne Bereiche, Eigenschaften, die eine seitliche Bewegung verursachen, ein Loch in der Nähe einer Kante usw. Bei einem maschinell gefertigten Teil könnten das unter anderem schmale Ecken, verdeckte Oberflächen oder nur mit einer Kugelmühle bearbeitbare, gekrümmte Oberflächen sein.
Mit Blick auf das unten abgebildete Teil sehen wir ein ähnliches Verhältnis von Material- zu Konversionskosten. Dieses Mal schauen wir uns jedoch die Eigenschaften genauer an, die die Fertigung komplex machen, da Gussverfahren oder Strangpressung keine Option sind.
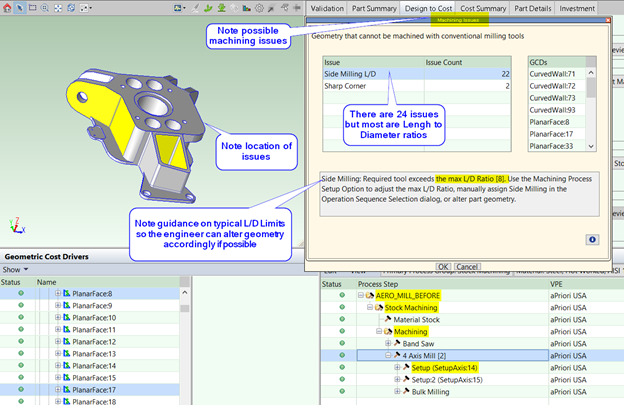
Aus Zeitgründen beschränken wir uns darauf, so viele dieser Länge-Durchmesser-Verhältnisse wie möglich zu lösen. Der Konstrukteur stellt fest, dass der Eckenradius dieser Fächer klein ist und damit kleine Werkzeugdurchmesser erfordert, die die üblichen Länge-Durchmesser-Verhältnisse missachten und die Endbearbeitung verlangsamen. Es steht ihm frei, diese zu vergrößern. Da sich die Menge des verbrauchten Materials dabei nicht unterscheidet, setzt er diese Änderung um. Das neu gestaltete Teil ist unten zu sehen.
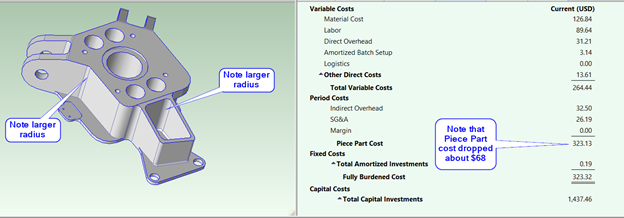
Größere Eckenradien ermöglichen die Wahl von größeren Durchmessern, sodass das Werkzeug weiter nach unten reichen kann ohne zu wackeln. Die Zyklusdauer wird verkürzt, die Kosten sinken. Während die Einsparung weniger beträgt als die 200 US$, die durch ein Gussverfahren eingespart werden, sind 17 % sicherlich den Aufwand einer Neukonstruktion wert.
Weitere potenzielle Methoden für kostenwirksames Design for Manufacturing
Auch die Maschinengröße lässt sich mit dem Design beeinflussen. Nehmen wir an, Sie arbeiten an einem Teil, das in China hergestellt wird. Die Lohnkosten sind daher niedrig, aber die Gemeinkosten sind hoch, denn das Teil wird auf einer großen, teuren Maschine produziert. Überlegen Sie, ob es Eigenschaften gibt, die sich auf die Maschinenwahl auswirken könnten.
In der Mitte des unten abgebildeten, druckgegossenen Teils findet sich ein Steg, der funktional gesehen nicht wirklich notwendig ist. Dieser Steg ist der Grund, warum das Teil zwei Seitenkerne benötigt –jeweils einen auf jeder Seite. Wenn der Steg entfernt werden würde, sollte nur ein Kern erforderlich sein. Die Formbasis wird kleiner und auch die Maschinengröße (Tonnage). Daraus ergibt sich eine Reduzierung der Werkzeug- und Werkstückkosten mit einer kleineren Maschine/geringeren Gemeinkosten. Weiterhin könnten Sie jetzt mit weniger Kavitäten auskommen, was ein großer Vorteil ist, wenn es sich um ein Teil mit hohem Produktionsvolumen handelt.
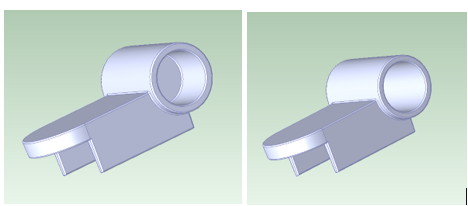
Die Anzahl der Einstellungen kann sich dramatisch auf die Kosten eines Teils mit niedrigem Produktionsvolumen auswirken. Ein Loch, dass nicht von einer bereits verfügbaren Einstellungsrichtung erreicht werden kann (aPriori kann Sie hier anleiten), kann eine gesonderte Einrichtung erfordern.
Zu viele davon erfordern eine teurere Maschine und beispielsweise einen Wechsel von einer 3-achsigen zu einer 4- oder 5-achsigen Fräse. Wussten Sie außerdem Folgendes? Wenn Ihr Feinblechteil sowohl eine Biegung mit einem spitzen Winkel als auch eine Biegung mit einem stumpfen Winkel beinhaltet, müssen dafür 2 Biegebrüche eingerichtet werden. Die Auswirkungen auf die Kosten sind bei einem hohen Produktionsvolumen minimal. Bei geringen Volumina kann sich dies jedoch als extrem unwirtschaftlich herausstellen.
Mehr erfahren
Wenn Sie mehr über die Nutzung der Digital Manufacturing Simulation für eine maßgebliche Verbesserung der Software-Ressourcen für Design for Manufacturability erfahren möchten, empfehlen wir Ihnen unser Webinar: The Exhausted Engineer.
In diesem Webinar erfahren Sie, wie die Produktionssimulation von aPriori für die Kostenkalkulation auch anspruchsvolle Automatisierung berücksichtigt, die Konstrukteur*innen eine erhebliche Menge an Zeit sparen kann. aP Generate, eine revolutionäre, neue Technologie für die digitale Fertigungssimulation, läuft unauffällig im Hintergrund und analysiert die digitalen Zwillinge Ihrer CAD-Modelle jedes Mal, wenn sie in Ihr PLM-System geladen werden, um proaktiv Empfehlungen zu potenziellen Kostenoptimierungen bereitzustellen.
Digital Twins Reimagine
Learn how manufacturing leaders and industry experts apply digital twins to drive profitability and sustainability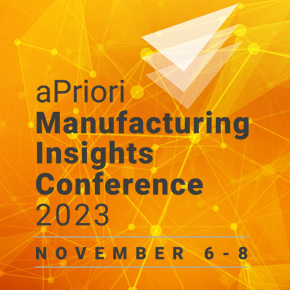
Abonnieren Sie den aPriori Blog
Mit technologiebasierten Lösungen ist eine strategische Materialbeschaffung möglich
25 September 2024Verwandeln Sie Meetings zur Überprüfung des Produktdesigns in schnelle Designvalidierungen
17 September 2024Wie KI-Tools die Kosten für die Produktentwicklung und die Markteinführungszeit senken
22 August 2024