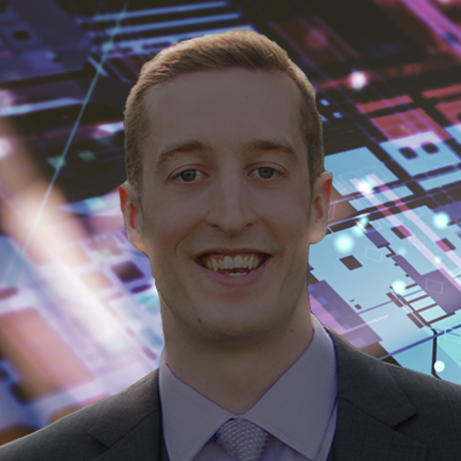
Transcript
Leah Archibald: Die Probleme in der Lieferkette, die die Elektronikhersteller in den letzten zwei Jahren geplagt haben, werden nicht verschwinden. Es gibt immer noch nicht genügend Chips, um den Bedarf all unserer intelligenten Geräte zu decken, und die Ingenieure mussten die aktuellen Produkte so umgestalten, dass sie die Komponenten verwenden, die sie vorrätig haben. Noch schlimmer ist, dass sie versuchen müssen, zukünftige Produkte zu entwerfen, ohne zu wissen, welche Komponenten verfügbar sein werden. Wie können Ingenieure den Anforderungen von heute gerecht werden und gleichzeitig der Chip-Knappheit von morgen einen Schritt voraus sein?
Mein Gast ist der Maschinenbauingenieur Sam Ellis. Er begann seine berufliche Laufbahn bei Raytheon und leitete Ingenieurteams bei Unternehmen wie Micross Components, die missionskritische Chips für Hersteller in der Verteidigungs-, Luft- und Raumfahrt- und Telekommunikationsindustrie liefern. Heute ist er hier, um darüber zu sprechen, wie Konstrukteure sich anpassen und in der neuen Welt der Fragezeichen-Komponenten erfolgreich sein können.
Sam Ellis, herzlich willkommen zu unserem Podcast.
Sam Ellis: Danke, dass ich dabei sein darf, Leah. Ich freue mich schon auf die heutige Sitzung.
Leah Archibald: Ich frage mich, ob Sie uns zu Beginn ein Beispiel dafür geben könnten, wie es aussieht, wenn die gemeinsame Nutzung von Daten wirklich funktioniert, um Teams bei der Anpassung an einen Mangel an Komponenten zu helfen.
Sam Ellis: Wenn ich mir ein Traumszenario ausdenken könnte, dann würde es so aussehen. Ich bin ein Entwicklungsingenieur. Ich arbeite an meiner Leiterplattenbestückung. Ich wähle meine Komponenten aus. Und ich lebe einfach in meiner Design-Software. Ich möchte das nicht verlassen. Außerhalb meiner bewussten Aufmerksamkeit gibt es ein System, das mit meiner Konstruktionssoftware verbunden ist. Während ich meine Stückliste zusammenstelle, extrahiert es alle Komponenten, die ich für meinen Entwurf ausgewählt habe. Es nimmt diese Komponenten und analysiert sie mit einem Tool zur Analyse der Lieferkette. Es prüft die Verfügbarkeit dieser Komponenten. Wie lange ist die Vorlaufzeit? Wie viele Lieferanten bieten sie an? Wie hoch ist das Risiko in der Lieferkette? Das alles geschieht automatisch im Hintergrund. Wenn dann problematische Komponenten an die Spitze kommen, wird der Beschaffungsspezialist alarmiert, und er kann seine wertvolle Zeit damit verbringen, nur die 5 % der Komponenten in der Stückliste zu prüfen, die problematisch sein werden. Dann können sie sich mit der Technik unterhalten: Schauen wir uns doch mal ein paar andere Optionen an. Gibt es eine Möglichkeit, andere Komponenten zu verwenden?
Leah Archibald: Mehr Informationsaustausch und mehr automatisierte Warnungen bedeuten also weniger manuelle Arbeit für den Konstrukteur. Und dann ruht weniger auf Ihren Schultern.
Sam Ellis: Ganz genau.
Leah Archibald: Gut, dann habe ich jetzt eine andere Frage: Wie können Konstrukteure mehr Flexibilität in die Entwürfe einbauen, die sie erstellen? Denn selbst im besten Fall wird es in der Zukunft Änderungen geben.
Sam Ellis: Die Designflexibilität wird weitgehend von der Funktion und dem letztendlichen Anwendungsfall des Produkts bestimmt. Als ich in der Verteidigungsindustrie gearbeitet habe, gab es eine Menge Beschränkungen. Dazu gehört, welche Bleimaterialien zulässig sind und welche Umweltanforderungen erfüllt werden müssen. Möglicherweise gibt es keine handelsüblichen Teile, die diese Kriterien erfüllen. Als Konstrukteur sollten Sie jedoch so weit wie möglich versuchen, kundenspezifische oder ausschließliche Komponenten zu vermeiden. Sie wollen sich nicht auf eine Option festlegen – Sie wollen in der Lage sein, mögliche Alternativen in der Stückliste anzugeben. Auch wenn man die Zukunft nicht vorhersagen kann, sollte man dem Beschaffungsteam oder dem Vertragshersteller so viel Vielfalt wie möglich in der Stückliste bieten, damit sie in einer sich verändernden Landschaft die verfügbaren Komponenten abrufen können.
Leah Archibald: Wie schwer ist es, über verschiedene Materialien oder Komponenten nachzudenken, die man verwenden könnte? Wie schwer ist es, diese Szenarien zu testen, und wie schwer ist es, ein Szenario gegen ein anderes auszuspielen, ohne die Gesamtqualität des Produkts zu beeinträchtigen?
Sam Ellis: Es gibt eine Reihe von Schwierigkeiten, und es kommt auf die Ebene der Komponenten an. Wenn ich ein passives Bauteil wie einen Widerstand oder einen Kondensator betrachte, reicht es oft aus, nur einen Wert und nicht eine bestimmte Teilenummer anzugeben. Es gibt Dutzende bis Hunderte von verschiedenen Herstellern, die alle ähnliche Komponenten herstellen, die diese Kriterien erfüllen können. In diesem Fall kann der Auftragsfertiger jedes beliebige dieser Bauteile beschaffen. Das wäre dann ein so genannter Drop-in-Ersatz. Wenn ich eine bestimmte Komponente spezifiziert habe und der Vertragshersteller diese nicht finden kann, kann er buchstäblich 10 andere Teilenummern besorgen und sie einfach einbauen, ohne dass es Probleme gibt. Es muss nicht zur Bewertung an die Technik zurückgegeben werden. Es wird perfekt funktionieren. Das ist das einfache Szenario.
Etwas komplizierter wird es bei den aktiven Komponenten wie den Mikroschaltungen. Für die Chips gibt es keine so vielfältige Lieferkette. Es gibt nicht so viele Hersteller. Die Herstellung dieser Art von Komponenten wird etwas schwieriger.
Leah Archibald: Was tun Sie also in diesen schwierigen Situationen?
Sam Ellis: Auch wenn es nicht so viele Hersteller gibt, produzieren sie im Allgemeinen immer noch eine Reihe von Werten oder eine Reihe von verschiedenen Kriterien für jede Komponente. Es könnte eine Komponente für die Automobilindustrie sein. Wenn Sie nicht in der Automobilbranche tätig sind, benötigen Sie vielleicht keine so hochwertige Komponente. Sie brauchen vielleicht nicht die umfangreichen Anforderungen auf dieser Ebene zu erfüllen. Sie könnten eine geringere Qualität verwenden, aber immer noch die Automobilqualität als Backup oder als Alternative haben.
Manchmal gibt es verschiedene Gehäusetypen. Ich habe einen Chip, der sich im Wesentlichen in dem Gehäuse befindet, das auf die Leiterplatte gesetzt wird. Dieser Chip hat alle Funktionen, die das Design benötigt, aber er kann auf verschiedene Arten verpackt werden. Ein gängiges Gehäuse ist ein 8-poliges SOIC, das eine oberflächenmontierte Komponente ist. Er könnte aber auch in einer anderen Art von Bauteil verpackt sein, das stattdessen als Durchgangsbohrung installiert wird. Das Problem dabei ist, dass es offensichtlich bevorzugte Gehäuse gibt. Ein Lieferant kann zwei- oder dreimal mehr von einem Gehäusetyp herstellen als von einem anderen. Letztendlich kommt es aber auf die Verfügbarkeit an. Wenn es eine bestimmte Verpackungsart gibt, die besser verfügbar ist, und Sie sich noch in einem frühen Stadium Ihres Designprozesses befinden, sollten Sie sich für diese entscheiden.
Leah Archibald: Einige Gehäuse werden aufgrund der Toleranzen in einer bestimmten Branche erforderlich sein, wie z. B. im Verteidigungs- oder Automobilbereich, wo die Toleranzen geringer sind, aber bei Konsumgütern ist das vielleicht kein so einschränkender Faktor. Sie können also bei Ihren ersten Entwürfen einige Spezifikationen für mehr Spielraum hinzufügen?
Sam Ellis: Ganz genau. Das ist etwas, das heute häufig vorkommt. Wenn die Beschaffungsabteilung ein bestimmtes Bauteil nicht finden kann, findet sie ein ähnliches. Sie hat vielleicht ein paar andere hohe Unverträglichkeiten, so dass sie in diesem Fall zurück zur Technik gehen und sagen: Hey, passt das noch zu unserem Design? Wenn ja, können wir das stattdessen verwenden?
Wenn ich also mein Produkt entwerfe, sollte ich diese Flexibilität einplanen, anstatt dies erst am Ende zu tun. Ich sollte den kleinsten oder größten Toleranzbereich angeben, der für meine Komponente akzeptabel ist. Das möchte ich als primäres Kriterium verwenden. Und dann kann ich Alternativen mit engeren Toleranzen oder höher spezifizierten Güten angeben, die immer noch eine Option sind. Vielleicht sind sie teurer, aber zumindest sind sie vorhanden, und die Beschaffung muss nicht noch einmal in die Konstruktion eingreifen – sie weiß, dass diese Komponente funktionieren wird und kann sie als Ersatz verwenden.
Leah Archibald: Wenn ich Ihnen also die Frage stelle, wie Sie Flexibilität in Ihre Designentwürfe einbauen, sagen Sie wörtlich, dass Sie Flexibilität einbauen. Wenn Sie zum Beispiel ein 3D-CAD-Modell erstellen, fügen Sie die Metadaten ein, die besagen: Das ist die Flexibilität.
Sam Ellis: So kann man es perfekt ausdrücken. Es gibt einen Begriff, der sich „Bill of Material Health“ nennt. Das ist auch ein guter Begriff, der mit dieser Flexibilität einhergeht. Je flexibler Sie in Ihrem Design sind, desto gesünder wird Ihre Materialliste sein, weil es eine Reihe von Produkten gibt, die Sie verwenden können.
Leah Archibald: Und wenn Sie diese Informationen in Ihrem Konstruktionssystem haben und diese Daten mit der Beschaffung teilen, dann entfällt der Schritt, dass die Beschaffung zur Konstruktion zurückgehen und sagen muss: Können Sie mir andere flexible Optionen nennen? Wenn Sie die flexiblen Bereiche buchstäblich von Anfang an einbauen, müssen Sie dieses Hin und Her nicht mehr machen.
Sam Ellis: Das ist genau richtig. Im Extremfall können Sie sich sogar für ein anderes Leiterplattendesign entscheiden. Sie haben vielleicht ein kritisches Bauteil, das nur ein einziger Lieferant herstellt. Also müssen Sie dieses Bauteil verwenden. Sie könnten zwei verschiedene Leiterplatten entwerfen, eine für Gehäusetyp A und eine für Gehäusetyp B, und so eine gewisse Flexibilität in Bezug auf Ihre kritische Komponente einbauen. Das wird nicht bevorzugt, weil es die Komplexität des Designs erhöht, aber es kann ein letzter Ausweg sein, wenn man auf ein kritisches Bauteil angewiesen ist.
Leah Archibald: Und es ist eine weitere Möglichkeit, dem Team Optionen für die Zukunft zu geben. Ihre erste Option auf der Ebene war: Kann ich es an einer ganzen Reihe von verschiedenen Orten auf der Welt machen. Ihre Option auf der zweiten Ebene war: Kann ich es in verschiedenen Verpackungen liefern? Und die dritte Option war: Wenn ich es nur über einen Lieferanten herstellen kann, kann ich es auf verschiedenen Maschinen oder mit verschiedenen Verfahren herstellen, so dass Ihr Lieferant diese Flexibilität hat.
Sam Ellis: Und wieder geht es darum, eine Art automatisiertes System einzurichten. Ein Konstrukteur möchte sich nicht hinsetzen und für jedes Bauteil in einer Stückliste mit 250 Komponenten 10 Alternativen finden. Das wäre reine Zeitverschwendung. Damit sind wir wieder bei der Bedeutung der Automatisierung. Verwenden Sie eine Lösung wie aPriori, die alle potenziellen Alternativen, die in Frage kommen, auflistet und dann eine Rangliste dieser Alternativen erstellt.
Leah Archibald: Ich höre den Vorteil, den eine wirklich robuste Plattform für Flexibilität und die Speicherung von Metadaten über Entwürfe den Ingenieuren bieten kann. Aber wenn Sie auf den Hersteller als Ganzes zurückblicken, welchen Wettbewerbsvorteil kann dieses System zur gemeinsamen Nutzung von Informationen dem Hersteller als Ganzem verschaffen? Denn wenn es darum geht, der weltweiten Chipknappheit einen Schritt voraus zu sein, dann geht es hier wirklich um die Wettbewerbsfähigkeit des gesamten Unternehmens.
Sam Ellis: Meiner Meinung nach läuft alles auf eine schnelle Markteinführung hinaus. Wenn man dieses System der Zusammenarbeit zwischen diesen beiden verschiedenen Gruppen einrichtet, haben beide Teams die Informationen, die sie brauchen. Sie müssen nicht zu viel Zeit mit manuellen Eingaben verbringen. Die Informationen sind nicht nur für die Technik und die Beschaffung, sondern auch für das Managementteam früher verfügbar. So kann ich zwar an einem Produkt arbeiten, aber das Managementteam wird mehrere verschiedene Produkte überwachen. Sie werden sehen können, ob es eine Möglichkeit gibt, die Liste der problematischen Komponenten zu konsolidieren. Diejenigen, die sie nicht loswerden können, erfahren wir bereits in der Entwicklungsphase, so dass wir nicht mit einer unvorhergesehenen 32-wöchigen Vorlaufzeit rechnen müssen, wenn wir an den Vertragshersteller gehen.
Leah Archibald: Wenn ich Sie also frage, was der Wettbewerbsvorteil ist, den ein Informationssystem dem Hersteller verschafft, sagen Sie, dass es kein neuer Wettbewerbsvorteil ist. Es ist derselbe alte Wettbewerbsvorteil – die Zeit bis zur Markteinführung – aber wir beschleunigen sie mit dieser neuen Technologie.
Sam Ellis: Ja, das ist perfekt. Ich hätte es selbst nicht besser formulieren können.
Leah Archibald: Nun, das war wirklich sehr aufschlussreich. Sam Ellis, vielen Dank, dass Sie heute bei mir im Podcast sind.
Sam Ellis: Es ist mir ein Vergnügen, hier zu sein. Danke, dass ich dabei sein durfte.
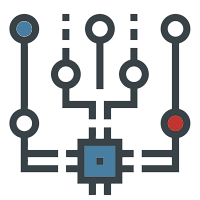