Unsere Erkenntnisse richten sich an ein breites Publikum – von Konstrukteuren bis hin zu Beschaffungsspezialisten – und stellen sicher, dass Sie über umsetzbare Daten verfügen, um Prozesse zu optimieren und die Rentabilität zu steigern. Durch den Einsatz moderner Schätzverfahren können Sie ein klareres Verständnis der Produktionskosten gewinnen und Effizienzsteigerungen im gesamten Fertigungsprozess erzielen. Um diesen umfassenden Leitfaden herunterzuladen, füllen Sie einfach das Formular aus!
Leitfaden jetzt herunterladen!
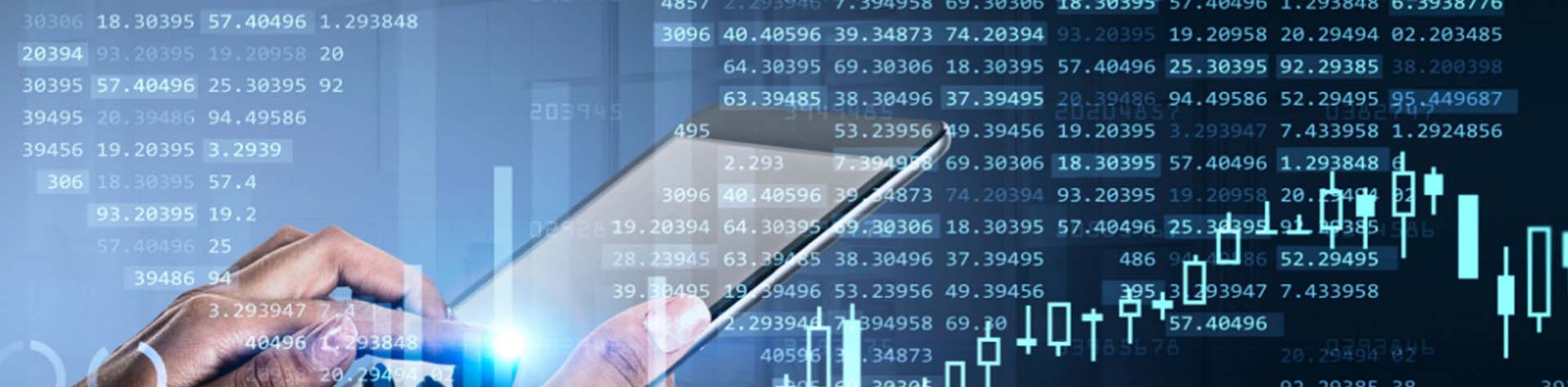
Was ist eine Herstellungskostenschätzung?
Die Schätzung der Herstellungskosten ist die Sammlung von Methoden und Werkzeugen, die zur Prognose der erwarteten Endkosten eines hergestellten Produkts verwendet werden.
Diese Analyse ermöglicht es Herstellern, wichtige Entscheidungen zu treffen, wie z. B. die Identifizierung profitabler Produkte, die Auswahl kostengünstiger Lieferanten und die Bestimmung, welche bestehenden Innovationen überarbeitet werden müssen, um wettbewerbsfähig zu bleiben. Mit der präzisen Fertigungskostenschätzung von aPriori können Unternehmen Änderungen in der späten Entwicklungsphase effektiv reduzieren und bessere Konditionen mit Lieferanten aushandeln.
Die Tiefe dieser Analyse kann von einfachen Überschlagsrechnungen bis hin zu umfassenden und präzisen simulationsgesteuerten Kostenmanagementplattformen wie aPriori reichen. Fertigungskostenschätzungen bilden eine wesentliche Grundlage für damit zusammenhängende Analysen, darunter:
Gründe für die Notwendigkeit: Die Kostenkalkulation ist für Hersteller heute unerlässlich
Da sich die Zeiträume für Produktentwicklung und Angebotserstellung verkürzen, nutzen Hersteller zunehmend fortschrittliche Kostenkalkulationsfunktionen, um Strategien für schlanke Produktion und Kostensenkung umzusetzen. Wenn sie mit diesen Strategien nicht Schritt halten können, wird es für sie schwierig, im globalen Wettbewerb zu bestehen.
Neue Technologien unterstützen diese neuartigen Kostensenkungsmethoden und ermöglichen diesen unermüdlichen Drang nach Kostenoptimierung. Mit der zunehmenden Verbreitung dieser Technologien scheint sich der Trend zu einer äußerst wettbewerbsorientierten Fertigung nur noch zu beschleunigen.
Um zu verstehen, wohin sich die Fertigung entwickelt und warum bessere Methoden zur Produktkostenschätzung eine Revolution vorantreiben, ist es hilfreich, kurz zu betrachten, wie Hersteller in der Vergangenheit Schätzungen durchgeführt haben.
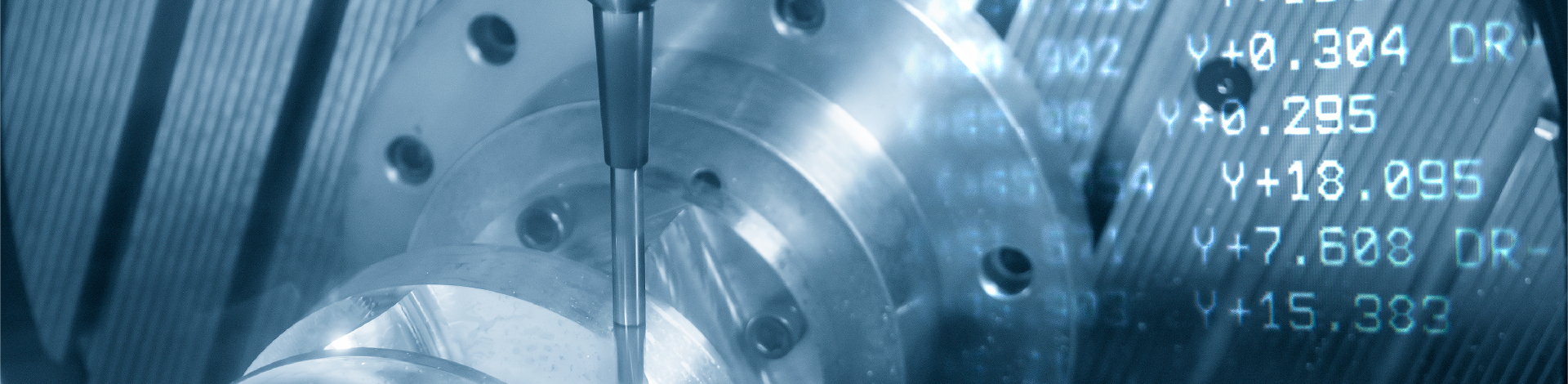
Die Entwicklung von Methoden zur Schätzung von Herstellungskosten
Jeder Produktionsbetrieb muss ein grundlegendes Verfahren zur Kostenschätzung anwenden, um die Rentabilität sicherzustellen. Dies beinhaltet oft die Berechnung der erwarteten Inputkosten auf der Grundlage der aktuellen Marktpreise und die anschließende Hinzufügung eines Aufschlags für Verpackung, Versand und Gewinn. Wenn die Schätzung die aktuellen Marktpreise übersteigt, ist die Produktion nicht rentabel.
Unternehmen verwenden für diesen Ansatz in der Regel selbst erstellte Datenbanken mit historischen Daten. Die Einführung von MS Excel im Jahr 1985 wurde zum gängigsten Tool für diese Kostenstrategien, insbesondere für kleine Lieferanten mit einigen wenigen Kostenkalkulatoren im selben Büro. Wenn jedoch Design, Fertigung und Beschaffung auf nationaler oder globaler Ebene verwaltet werden, wird es zu komplex, die extreme Anzahl von Kostenvariablen in einer Tabelle zu verwalten.
Direkte Kosten wie Löhne und Rohstoffe hängen von der Effizienz des Produktionsprozesses ab und variieren bei der Schätzung von Designalternativen.
Anfang bis Mitte der 1980er Jahre kam eine spezielle Software zur Kostenschätzung auf den Markt, die für Fertigungskostenschätzer entwickelt wurde. Für die effektive Nutzung dieser Software war eine umfassende Schulung erforderlich. Diese frühen Systeme, die nicht auf moderner Datenbanktechnologie basierten, stellten die Mitglieder von Design- und Beschaffungsteams in verschiedenen Regionen oft vor erhebliche Herausforderungen bei der Konsistenz der Kostenmodelle.
Anfang der 2000er Jahre suchten Hersteller nach Systemen zur Schätzung der Herstellungskosten, mit denen Designer und Ingenieure schnell feststellen konnten, ob ein neues Design, das durch ein solides 3D-CAD-Modell dargestellt wird, die Zielkosten in den frühen Phasen des Designprozesses erfüllt. Auch Beschaffungsmanager erkannten den Wert von Kostenschätzungen, die detaillierte Einblicke in die Fertigung für bessere Lieferantenverhandlungen bieten. Kostenschätzungsteams, die in der Regel unterbesetzt sind, benötigten automatisierte Systeme für Aufgaben wie die Chargenkalkulation von CAD-Modellen, um Kostenausreißer zu identifizieren. Die sich entwickelnden Anforderungen treiben Hersteller zu Lösungen mit moderner Datenbankarchitektur, die über einen Webbrowser verfügbar ist und mit umfangreichen Bibliotheken von Material- und Maschinendaten ausgestattet ist.
Modernste Systeme zur Fertigungskostenschätzung, wie aPriori, bieten drei Automatisierungsebenen, darunter:
- Teil-/Baugruppen-3D-CAD-Geometrieanalyse: Erhalten Sie sofortige Kostenschätzungen und Feedback zur Herstellbarkeit von 3D-CAD-Modellen
- Massenkostenanalyse: Effiziente Bewertung mehrerer Teile/Baugruppen zur Ermittlung von Kosteneinsparungsmöglichkeiten
- PLM-Integrationsbasierte Analyse: Optimieren Sie Arbeitsabläufe durch die Integration automatisierter Designanalysen und umsetzbarer Erkenntnisse in das Product-Lifecycle-Management-System (PLM)
Lean Manufacturing: Ein ganzheitlicheres Konzept von Kosten, Verschwendung und Wert
Das Mitte der 1980er-Jahre eingeführte Lean Manufacturing entwickelte sich zu einer Strategie zur Kostenoptimierung, da in der US-amerikanischen Geschäftswelt weit verbreitete Besorgnis über die unüberwindliche Effizienz japanischer Hersteller herrschte. Wirtschaftsführer auf der ganzen Welt versuchten, die Methoden, die den Erfolg Japans begründeten, zu erlernen und zu imitieren. In weniger als 40 Jahren, nachdem der Industriesektor durch den Zweiten Weltkrieg völlig am Boden lag, wurde Japan zum Neidobjekt der Hersteller weltweit, die die Schlüssel zu seiner Effizienz aufdecken mussten.
Im Kern konzentriert sich die schlanke Produktion auf die Beseitigung von Verschwendung oder Muda in einem Fertigungsunternehmen. Diese Verschwendung kann ungenutzte Materialien, unverkaufte Produkte und alle Kosten umfassen, die nicht direkt zum Wert des Endprodukts beitragen. Darüber hinaus umfasst diese Verschwendung untätige Mitarbeiter, die auf Lieferungen warten, übermäßige Versandzeiten aus länderübergreifenden Lagern und unverkaufte Nebenprodukte oder Ausschuss.
Während die Erfolge japanischer Hersteller dazu beitrugen, den Begriff „Lean“ bekannt zu machen, sind die weitreichenden Vorteile der Abfallvermeidung und die Risiken der Ineffizienz aufgrund unzureichend analysierter Verfahren und Designentscheidungen für zukunftsorientierte Hersteller schon lange ein Thema.
Henry Ford, ein Pionier der Massenproduktion, betonte in seiner Autobiografie, wie wichtig es ist, Ineffizienzen zu erkennen, um die Kosten besser kontrollieren zu können. Er äußerte die Ansicht:
„Ich glaube, dass der durchschnittliche Landwirt nur etwa 5 % der aufgewendeten Energie für einen sinnvollen Zweck einsetzt … Nicht nur, dass alles von Hand gemacht wird, es wird auch selten über eine logische Anordnung nachgedacht. Ein Landwirt, der seine Arbeit erledigt, wird ein Dutzend Mal eine wackelige Leiter hinauf- und hinuntergehen. Er wird jahrelang Wasser tragen, anstatt ein paar Rohrstücke zu verlegen.“
Für Fords Farmer war die Erkennung des Potenzials für Prozessverbesserungen und Kapitalinvestitionen der Schlüssel zu einem besseren Kostenmanagement. Heute ist die Ermittlung der Kosten in der Fertigung jedoch weitaus komplexer. Sie umfasst eine eingehende Bewertung jedes Produktkostenelements und seiner Beziehung zu Merkmalen wie Form, Passform und Funktion sowie der Prozessanforderungen für Fertigung, Beschaffung und Vertrieb.
Ohne fortschrittliche Technologie kann keine noch so gründliche Studie das komplexe Zusammenspiel zwischen technischen und geschäftlichen Variablen genau abschätzen.
Technologie für Kalkulationssysteme: Der Schlüssel zur Beschleunigung und Verbesserung der Kostenschätzung
Hersteller haben immer wieder neue Technologien eingesetzt, um zumindest eine vage Annäherung an die komplexen Variablen zu erhalten, die in den Endkosten eines Produkts zusammengefasst sind. Bessere Kostenschätzungsverfahren waren schon immer an technologische Möglichkeiten gebunden. In der Geschichte der Fertigung war die Kostenschätzung meist eine Frage langsamer und stetiger Experimente.
Technologien, vom Personal Computer bis hin zur Unternehmens-Tabellenkalkulation, haben diese Experimente effizienter gemacht und die Berücksichtigung rechenintensiverer Variablen ermöglicht. Diese traditionellen Verfahren zur Kostenschätzung sind jedoch immer auf irgendeiner Ebene vage und ad hoc. Komplexe Variablen werden durch praktische (aber letztlich ungenaue) Methoden abstrahiert, wie z. B. den Vergleich mit ähnlichen Projekten aus der Vergangenheit oder die Zuweisung linearer Stückkosten zu den verwendeten Materialien.
Eine Sammlung von Excel-Tabellen zur Erfassung von Komponenten- und Arbeitskosten ist sicherlich besser als der Rückgriff auf eine allzu vereinfachte Kosten-plus-Preisgestaltung. Aber Tabellenkalkulationssoftware ist nicht wirklich in der Lage, Schätzungen mit Entscheidungen auf Entwurfsebene zu verknüpfen. Diese Fähigkeit ist Herstellern erst mit dem Aufkommen von Technologien zur Fertigungskostenrechnung zugänglich geworden, die Analysen auf technischer Ebene mit umfassenderen Kostenmanagementaspekten wie Lieferkette, Herstellbarkeit und Arbeitskosten integrieren.
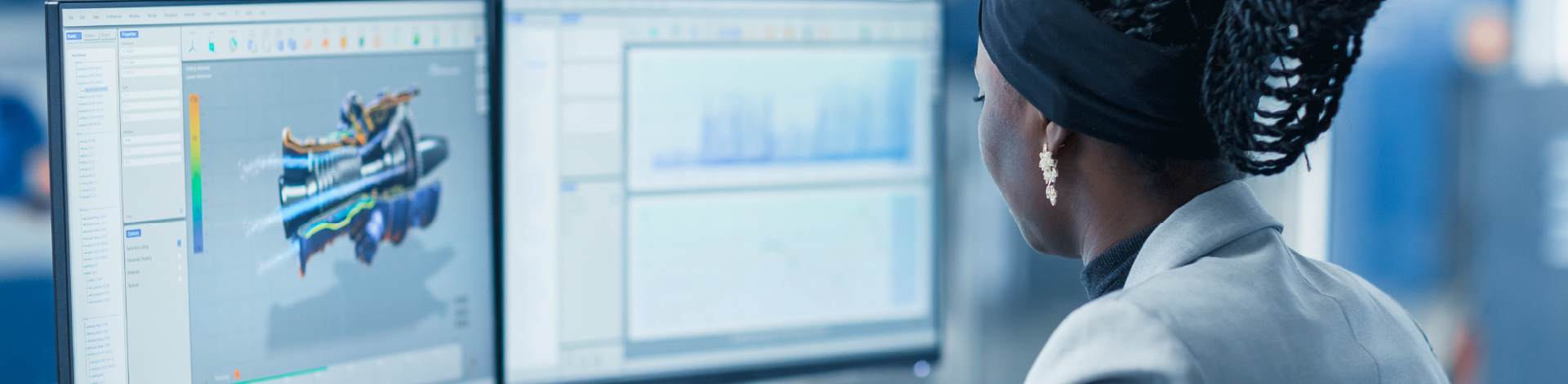
Der signifikante Anstieg von Software zur Schätzung von Herstellungskosten
Der Erfolg innovativer Kostensenkungsstrategien wie der schlanken Produktion ist untrennbar mit einer erfolgreichen Fertigungskostenschätzung verbunden. Um festzustellen, welche Kosten letztendlich den Wert beeinflussen, benötigt ein Hersteller eine Plattform, um sie mit den funktionalen Merkmalen eines Produktdesigns zu verknüpfen.
Genau das kann die fortschrittlichste Software zur Fertigungskostenschätzung bieten: eine simulationsgesteuerte Analyse aller Aspekte der Kostenstruktur eines Produkts. Diese Analyse ist in wenigen Minuten oder weniger verfügbar und liefert Designern umsetzbare Kostendaten zur Anatomie der Produktkosten. Diese umfassende Buchführung muss Details wie die Kosten für Rohmaterialien, Materialnutzung, Rückkauf von Ausschuss, gekaufte Teile/Komponenten, Werkzeugkosten, Arbeitskosten, Maschinenabschreibung und eine Vielzahl indirekter, anlagenbezogener Kosten enthalten.
Eine moderne Technologie zur Schätzung der Herstellungskosten sollte eine rollenbasierte Benutzererfahrung beinhalten, die von allen wichtigen Interessengruppen im Produktentwicklungsprozess genutzt werden kann, darunter:
Produktdesigner und Ingenieure
Beschaffungs-, Einkaufs- und Supply-Chain-Manager
Fertigungskostenschätzer
Diese komplexen Analysefunktionen ergeben zusammen ein Toolkit, das nicht nur die Kostenschätzung eines Produkts schneller und genauer macht (obwohl die richtige Software dies sicherlich leistet), sondern es Designern auch ermöglicht, Alternativen mit soliden Kosten zu erkunden, während ein Produkt noch in der Entwurfsphase ist. Die Möglichkeit, dynamische, simulationsgesteuerte Kostenschätzungen in den Designprozess selbst zu integrieren, ermöglicht es Herstellern, ihre Einstellung zu Kosten zu ändern.
Die richtige Technologie ermöglicht es, Kosten nicht als Ad-hoc-Grenze für das Produktdesign zu betrachten, sondern als unabhängige Variable des Designprozesses selbst.
Als die simulationsgesteuerte Schätzung erstmals technisch möglich wurde, war sie nur die Domäne engagierter Experten für computergestützte Technik. Der Markt hat jedoch eine rasche Demokratisierung der Simulation erlebt, mit Anbietern wie aPriori, die fortschrittliche Software zur Kostenschätzung anbieten, die von Produktdesignern und Kostenexperten gleichermaßen genutzt werden kann.
Da dieser designorientierte Ansatz zur Kostenschätzung immer mehr Einzug in die tägliche Praxis von Herstellern auf der ganzen Welt hält, entstehen immer mehr Strategien, die auf dieser Fähigkeit basieren. Die wichtigste ist „Design to Cost“.
Design to Cost (DTC): Einführung robuster Schätzverfahren in den Designprozess
Design to Cost (DTC) ist eine Organisationsmethodik, die das Kostenmanagement in die Entscheidungsfindung während der frühen Entwurfsphase integriert, wie in unserem Artikel erläutert. Der DTC-Ansatz entfernt sich von konventionellen Methoden, die auf willkürlichen Kostensenkungszielen basieren. Stattdessen arbeiten Produktmanager mit Designern und Ingenieuren zusammen, um ein spezifisches Kostenziel für die Einführung eines neuen Produkts (NPI) festzulegen. Dieses Ziel basiert auf den aktuellen Marktbedingungen und zielt darauf ab, die Rentabilität zu maximieren.
Dieses Kostenziel ist in der Software zugänglich und ermöglicht es den Designern, schnell neue Fertigungskostenschätzungen zu erstellen, während sie dem Modell eine neue Detailebene hinzufügen, wodurch die Identifizierung und Beseitigung von Kostentreibern erleichtert wird. Folglich ermöglicht dieser Prozess dem Produktteam, Kosten- und Rentabilitätsziele konsequent mit Präzision und Zuversicht zu erreichen.
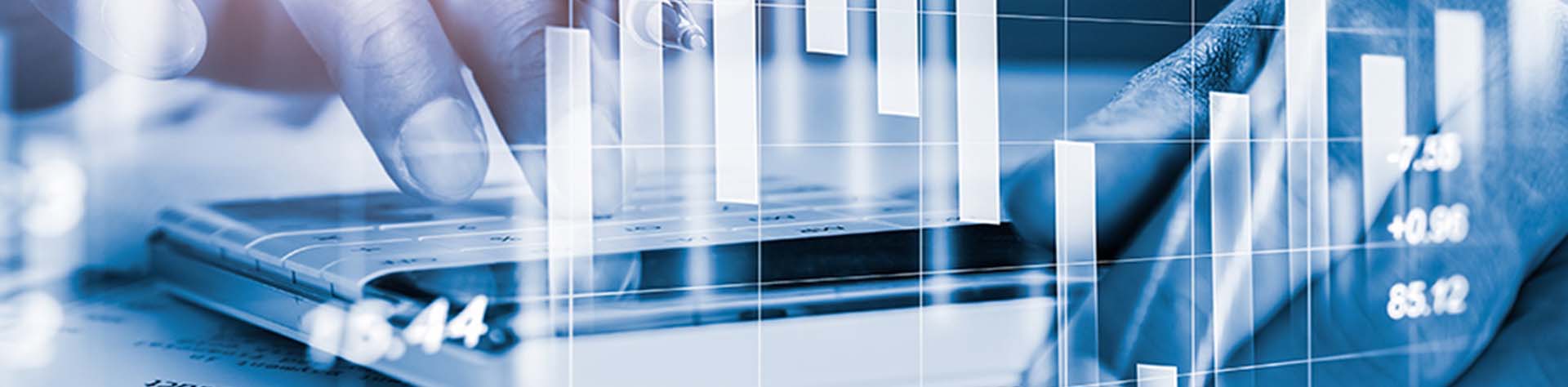
Produktkostentreiber im Blick behalten
Es ist von entscheidender Bedeutung, die Kosten als echte, vollständig quantifizierte Entwurfsvariable zu betrachten, da Designentscheidungen etwa 80 % der Kosten eines Produkts festlegen. Dies umfasst nicht nur die direkten Kosten für bestimmte Materialien, sondern auch eine Reihe von Sekundärkosten.
Während wir diese Kostentreiber in direkte und sekundäre Kategorien unterteilen, liegt der Schlüssel zu einem soliden Kostenansatz darin, die komplexen Zusammenhänge zwischen ihnen zu erkennen und zu bewerten. Die Wahl eines komplexeren Bearbeitungsprozesses, der die Auslagerung in ein Land mit höheren Zöllen, aber niedrigeren Lohnkosten erfordert, wirft beispielsweise wichtige Fragen auf, darunter:
- Ist dies eine intelligente Geschäftsentscheidung?
- Könnte das Teil durch eine Änderung des Designs, die diesen Bearbeitungsprozess überflüssig macht, vor Ort hergestellt werden?
Hersteller müssen sich heute mit solchen Fragen auseinandersetzen, die sich nicht einfach mit einer Tabellenkalkulation lösen lassen.
Beispiele für die wichtigsten Kostentreiber in der Fertigung
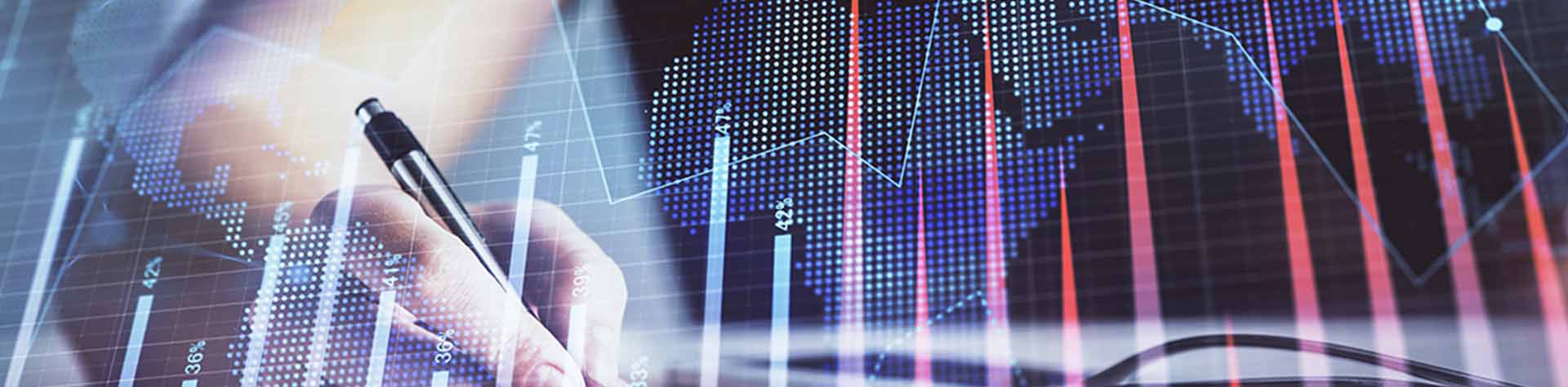
Wie man Produktkosten erfolgreich schätzt
Der erste Schritt bei der Kostenschätzung besteht darin, die aktuellen Produktionsteile zu bewerten, um Möglichkeiten für Verhandlungen oder eine Umgestaltung zu ermitteln, mit denen die Produktkosten gesenkt werden können.
Diese Bewertung muss Richtwerte für die effizienten Kosten eines Bauteils generieren. Diese Richtwerte lassen sich in zwei übergeordnete Kategorien einteilen:
Fertigungskostensysteme schätzen die Kosten, die ein Bauteil „kosten sollte“, wenn es effizienten Fertigungsprozessen folgt, genau ab. Zwar ist nicht jeder Lieferant vollkommen effizient, doch ermöglicht diese Analyse den Herstellern, erhebliche Diskrepanzen zwischen den von ihnen gezahlten Ist-Kosten und den von ihrer Software zur Fertigungskostenschätzung generierten Soll-Kosten zu ermitteln. Diese Diskrepanz kann durch einen ineffizienten Lieferanten oder einen Konstruktionsfehler verursacht werden, der zu überhöhten Kosten führt.
Nachdem Sie Kostenausreißer identifiziert haben, können Sie diese durch eine Neukonstruktion oder Neuverhandlung reduzieren. In unserem Artikel über die Senkung der Herstellungskosten werden zahlreiche potenzielle Einsparungsmöglichkeiten untersucht.
Zu den Vorteilen einer Sollkostenanalyse und -schätzung gehören:
- Identifizierung von Kostenausreißern und Verbesserung der Zusammenarbeit mit Lieferanten, um Kosteneinsparungen zu erzielen
- Erstellung interner Schätzungen und schnelle Bewertung von Design- und Fertigungsalternativen
- Optimierung der Beschaffungsvorgänge durch genaue Schätzungen
- Priorisierung von Designiterationen durch Anwendung einer Kostenausreißeranalyse
Wir bieten auch einen detaillierteren Leitfaden für die Durchführung einer Ausgabenanalyse an.
Als hochrangige Technik zur Identifizierung von Designineffizienzen generiert dieser Ansatz die erwarteten Kosten bei einer ähnlichen Masse, Materialspezifikation und einem ähnlichen Herstellungsprozess. Wenn eine Komponente stark von dieser Erwartung abweicht, ist es wahrscheinlicher, dass unnötig komplexe Designentscheidungen getroffen wurden.
Kostensysteme Technologie: Die wichtigste Beschränkung bei der Kostenschätzung Geschwindigkeit und Qualität
Um während der Entwurfsphase Kostenanalysen zu erstellen, muss Ihre Software zur Fertigungskostenschätzung extrem schnell und benutzerfreundlich sein.
Bei aPriori beginnt die Analyse beispielsweise mit dem Import einer 3D-CAD-Datei. Nach der Angabe einiger grundlegender Eingaben wie Produktionsvolumen, Fertigungsprozess und Fertigungsstandort kann aPriori in Sekundenschnelle eine umfassende Fertigungskostenschätzung erstellen.
Wenn Änderungen am CAD-Entwurf (oder an der Auswahl der Fertigungs-/Lieferkette) vorgenommen werden, können innerhalb weniger Sekunden neue Schätzungen erstellt werden, um sicherzustellen, dass das Designteam die festgelegten Kostenziele einhält. Die Möglichkeit, mithilfe der simulationsgesteuerten Kostenrechnung schnelle Analysen alternativer Szenarien durchzuführen, ist unerlässlich, um den Designprozess zu unterstützen, ohne die Ingenieure zu sehr zu belasten. Um die kostengünstigste Option zu generieren, sind Schätzungsplattformen unerlässlich, die in der Lage sind, jeden Produktionsprozess zu analysieren, der in jedem potenziellen Routing verwendet wird.
Techniken zur Produktkostenschätzung: Umfassende Tools für eine optimale Kostenschätzung
Costing systems technology: The main limitation in estimating cost, speed and quality
To perform cost analysis during the design phase, your manufacturing cost estimation software must be extremely fast and easy to use.
For example, with aPriori, the analysis starts with the import of a 3D CAD file. After entering a few basic inputs such as production volume, manufacturing process and manufacturing location, aPriori can generate a comprehensive manufacturing cost estimate in seconds.
As changes are made to the CAD design (or manufacturing/supply chain choices), new estimates can be generated in a few seconds to ensure that the design team is meeting established cost targets. The ability to perform rapid analysis of alternative scenarios using simulation-driven costing is essential to supporting the design process without overburdening engineers. To generate the most cost-effective option, estimation platforms are essential that are able to analyse every production process used in every potential routing.
Laden Sie unser Datenblatt herunter, um die vollständige Liste der von aPriori verwendeten Modelle zu erhalten.
Der letzte Schritt, um den vollen Wert der Erkenntnisse aus Ihrer Software zur Fertigungskostenschätzung zu realisieren, ist ein Kulturwandel hin zu einer kostenbewussten Produktentwicklungskultur. Ingenieure sind darauf trainiert, zuerst an Funktionalität und Zuverlässigkeit zu denken, und das Kostenmanagement in der Entwurfsphase stellt eine zusätzliche analytische Komplexität dar.
Die Bereitschaft, ein Produkt von Grund auf neu zu überdenken, ist unerlässlich, um die aussagekräftigste Schätzung zu erstellen.
Für einen umfassenden Überblick über unsere fast 90 RDLsladen Sie unser Datenblatt herunter.
Beispiele aus der Praxis für die Produktkostenschätzung
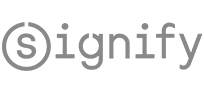
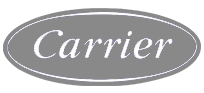
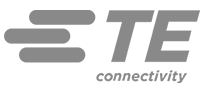
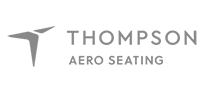
Increasing Should Cost Analysis by 8x to Digitalize Procurement
Signify ist der weltweit führende Anbieter von Beleuchtung für Verbraucher, Fachleute und das Internet der Dinge (IoT). Das Unternehmen hat sich erstklassigen Beschaffungspraktiken verschrieben, um optimale Kosten, Qualität und Verfügbarkeit von Komponenten zu gewährleisten. Um seine Fähigkeit zur Erstellung von Soll-Kostenanalysen für Produkte externer Anbieter zu verbessern, erkannte Signify die Notwendigkeit einer Automatisierung.
Das Unternehmen schloss sich mit aPriori zusammen, um Soll-Kostenmodelle für mechanische Teile zu erstellen, ein Ansatz, der den Beginn einer erfolgreichen digitalen Beschaffungsstrategie ankündigte.
Ergebnis(se): Mit der automatisierungsgesteuerten Plattform von aPriori erreichte Signify sein Ziel, die Sollkostenanalyse um das Achtfache zu erhöhen, und konnte so die Kosten für ein vielfältiges Produktportfolio optimieren.
Erfahren Sie mehr darüber, wie aPriori die Leistung und Effizienz des Kostenmanagements steigert.
Im Folgenden werden einige weitere Beispiele aus der Praxis für eine hervorragende Produktkostenschätzung vorgestellt.
Einsparungen von bis zu 30 Millionen US-Dollar bei kritischen Projektkosten
Carrier stellt Produkte in drei Hauptmarktsegmenten her: HLK (sowohl für den Wohn- als auch für den Gewerbebereich), Kältetechnik und Brandschutz/Sicherheit.
Die Kostenabteilung des Unternehmens implementierte aPriori zunächst, doch hat sich die Software inzwischen zu einer Kerntechnologie in den Bereichen Konstruktion und Beschaffung entwickelt.
Ergebnis(se): Mit der leistungsstarken Kostenmanagement-Plattform von aPriori und ihrer Rolle bei der Erzielung erheblicher finanzieller Vorteile prognostiziert Carrier Einsparungen von etwa 30 Millionen US-Dollar bei kritischen Produktentwicklungsprojekten.
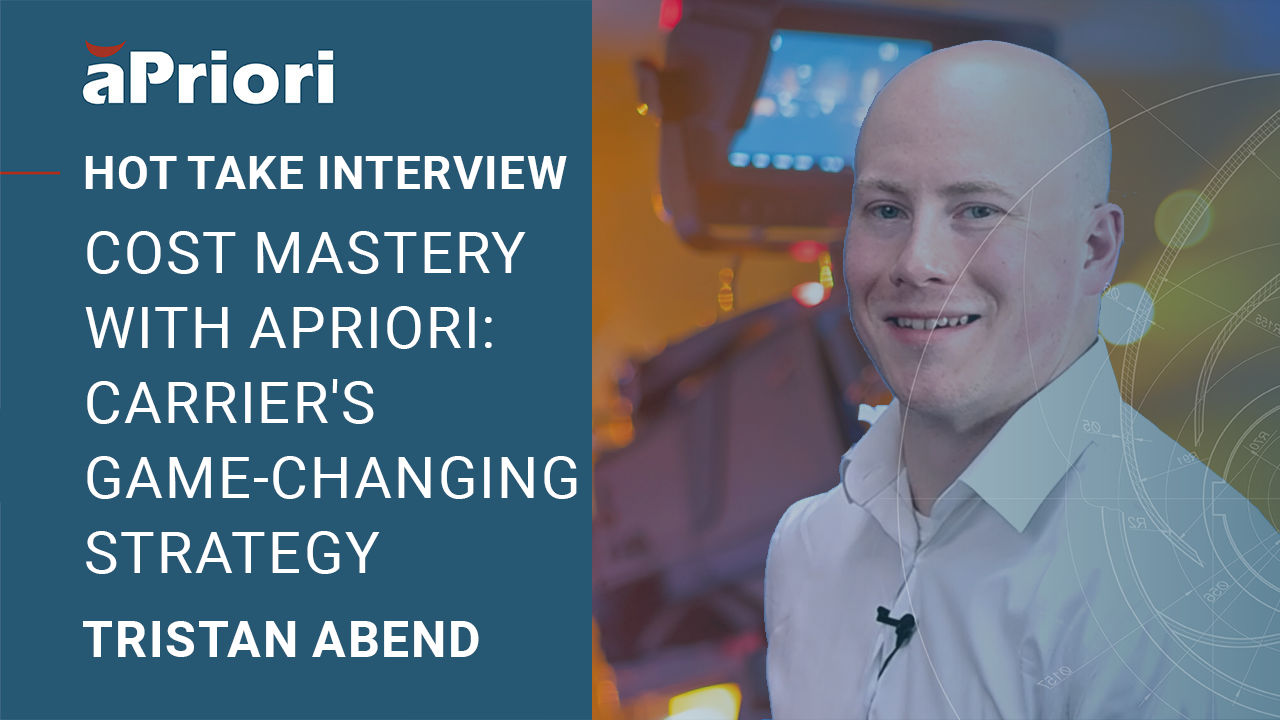
Zweistellige Kostensenkungen durch fundierte Zusammenarbeit mit Lieferanten
TE Connectivity, ein weltweit führender Anbieter von Steckverbindern und Sensoren, produziert jährlich mehr als 236 Milliarden Produkte in den Bereichen Kommunikation, Industrie und Transport.
Das Unternehmen sah sich in seinen Lieferantenpartnerschaften mit drei großen inflationsbedingten Kostenherausforderungen konfrontiert, darunter:
- Die Energiekosten stiegen um 300 %, was zu einem Anstieg der Maschinenrate eines Lieferanten um 10 % führte
- Die Produktionskosten stiegen in den letzten drei Jahren um 30 %.
- Die Lohn- und Fertigungskosten im Land eines Lieferanten waren doppelt so hoch wie der regionale Durchschnitt.
Um diese Probleme anzugehen, nutzte das Beschaffungsteam von TE Connectivity die Fähigkeiten von aPriori für eine genaue Kostenschätzung und eine Sollkostenanalyse. Dieser Ansatz lieferte ihnen detaillierte Einblicke in die Gesamtkostenstruktur eines Lieferanten und erleichterte erfolgreiche Verhandlungen über Kostensenkungen.
Ergebnis(se): TE Connectivity konnte jede Herausforderung mit aPriori bewältigen, was zu folgenden Ergebnissen führte:
- Die Erhöhung der Maschinenrate um 10 % wurde als unangemessen erachtet und wirkte sich nur zu 4 % auf die Produktkosten aus
- Es wurde eine Senkung der Rohstoffkosten um 15 % ausgehandelt, wodurch die anfängliche Erhöhung ausgeglichen wurde
- Die Verhandlungsmacht wurde gestärkt, was zu einer Senkung der Arbeits- und Herstellungskosten führte
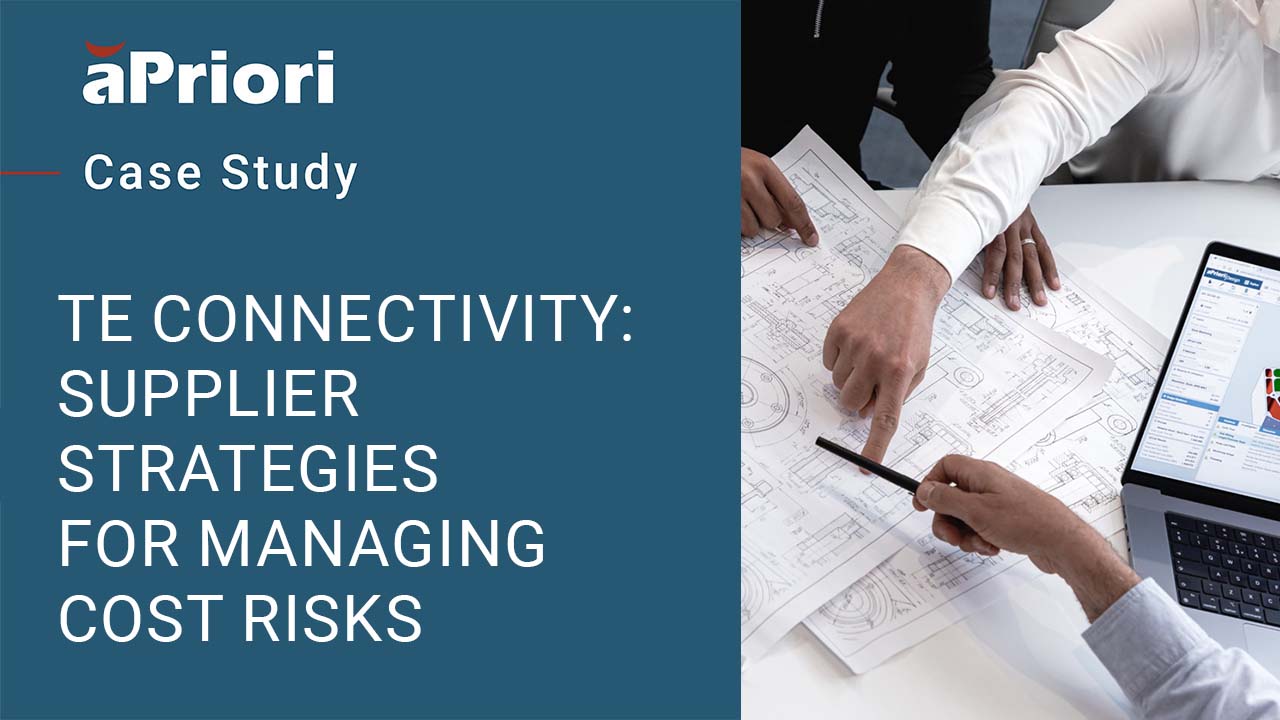
Analyse der Sollkosten zur Einsparung von 40 % bei den 50 teuersten Teilen
Thompson Aero Seating, ein auf Premium-Flugzeugsitze für Reisende der First- und Business-Class spezialisiertes Unternehmen, setzt die Sollkostenanalyse von aPriori ein, um die tatsächlichen Kosten seiner 50 teuersten lagerhaltigen Maschinenteile zu ermitteln. Das Beschaffungsteam des Unternehmens nutzte diese Sollkostenaufschlüsselungen für produktive Gespräche mit Lieferanten.
Ergebnis(se): Innerhalb von zwei Monaten nach der Einführung von aPriori konnte Thompson Aero Seating die Kosten für seine 50 teuersten bearbeiteten Teile um beeindruckende 40 % senken.
Nächste Schritte: Auf dem Weg zu einer neuen Ära in der Fertigung
Die globale Fertigungsindustrie beginnt gerade erst, das volle Potenzial moderner Kostenkalkulationstechnologien auszuschöpfen. Da diese Technologien immer mehr Verbreitung finden, werden Marktführer, die sie effektiv nutzen, wahrscheinlich den Kosten- und Preisdruck auf ihre Konkurrenten erhöhen. Wir können davon ausgehen, dass die Produktherstellung in absehbarer Zukunft weiterhin sehr wettbewerbsintensiv bleiben wird: Jede verpasste Gelegenheit zur Kostenoptimierung stellt eine potenzielle Bedrohung für den Marktanteil dar.
Es ist von entscheidender Bedeutung, die richtige Software für die Fertigungskostenberechnung auszuwählen, um sich auf diesem Markt zurechtzufinden und umsetzbare Kostenschätzungen in der von den Kunden von heute geforderten Geschwindigkeit zu erstellen. Weitere Informationen zu den wichtigsten Funktionen einer Kostenmanagement-Plattform für maximale Geschäftswirkung finden Sie in unserem Artikel über die wichtigsten Funktionen, auf die Sie bei einer Software zur Kostenschätzung achten sollten.
aPriori bietet umsetzbare Erkenntnisse für eine bessere Schätzung der Herstellungskosten
aPriori arbeitet mit Herstellern zusammen, um simulationsgesteuerte Kostenschätzungen in ihren Designprozess zu integrieren, sodass Unternehmen ihre Kosten unabhängig verwalten können. Die Plattform verbessert die Transparenz in der Fertigung und ermöglicht „Was-wäre-wenn“-Szenario-Bewertungen in Echtzeit, um kostengünstige Lieferanten, Materialien und Produktionsmethoden zu ermitteln.
aPriori bietet umsetzbare Erkenntnisse und detaillierte Daten und stellt sicher, dass zukunftsorientierte Hersteller durch ein effektives Fertigungskostenmanagement hervorragende Produkte erzielen.